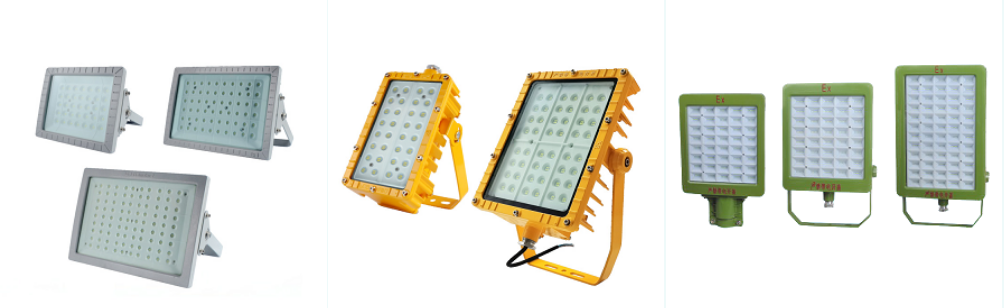
Intrinsic Safety vs Flameproof Design: Which Lighting Solution Dominates Petrochemical Zones?
Evaluating Safety, Compliance, and Efficiency in High-Risk Environments
Introduction: The Critical Choice in Petrochemical Lighting
In petrochemical facilities, where volatile gases like methane, hydrogen sulfide, and ethylene are prevalent, selecting the right hazardous area lighting is a matter of operational safety and regulatory compliance.
Two primary approaches dominate this space: intrinsically safe (IS) systems, which limit energy to prevent ignition, and flameproof (Ex d) designs, which contain explosions within rugged enclosures.
This article analyzes their technical distinctions, certification requirements, and real-world performance in petrochemical zones, providing actionable insights for engineers and safety managers.
1. Core Technical Differences: Energy Limitation vs Explosion Containment
A. Intrinsic Safety (IS)
Principle: Limits electrical and thermal energy to levels below what is required to ignite flammable atmospheres (typically <1.3W, <29V, and <300mA).
Applications: Ideal for low-power devices like gas detectors, sensors, and LED indicators in Zone 0/1 areas where explosive gases are continuously present.
Advantages:
Permits live maintenance without plant shutdowns.
Eliminates heavy enclosures, reducing installation costs by 30–50%.
B. Flameproof Design (Ex d)
Principle: Uses robust enclosures (cast steel or aluminum) to contain internal explosions and prevent external ignition.
Applications: Suited for high-power lighting (e.g., floodlights, halogen lamps) in Zone 1/2 environments with intermittent gas exposure.
Advantages:
Handles higher energy loads (e.g., 100W+ LEDs for refinery pipeline illumination).
Flameproof Complies with NEC Division 1 standards for North American petrochemical plants.
Key Contrast:
Risk Mitigation: IS prevents ignition, while Ex d controls explosions post-ignition.
Power Limitations: IS cannot support high-intensity lighting, whereas Ex d fixtures often require complex cooling systems to manage heat.
2. Certification and Regional Compliance Challenges
A. Global Standards
ATEX/IECEx: Mandate dual certification for IS (Ex ia/ib/ic) and Ex d (Ex d) in Zone 0/1. For example, IS lighting in European LNG terminals requires EN 60079-11 certification, while Ex d fixtures must pass cyclic pressure tests per EN 60079-1.
NEC/UL: Prioritizes Ex d for Division 1 zones but lacks explicit IS requirements for dust environments (NFPA 70), creating gaps in hybrid gas/dust facilities.
B. Petrochemical-Specific Requirements
Zone 0 (Continuous Hazard): Only IS (Ex ia) is permitted, as seen in offshore oil rig gas detection systems.
Zone 1 (Intermittent Hazard): Ex d dominates for high-power applications (e.g., refinery floodlights), while IS is used for control panels and sensors.
3. Operational Efficiency and Cost Analysis
A. Installation Costs
IS Systems: Lower upfront costs due to lightweight components and standard cabling, but require certified barriers (e.g., Zener diodes) and strict system design.
Ex d Systems: Higher initial investment (40–60% more than IS) due to heavy enclosures and explosion-proof conduits.
B. Maintenance and Lifespan
IS: Enables real-time diagnostics and repairs without shutdowns, reducing downtime costs by 25%.
Ex d: Quarterly torque checks and infrared inspections add $1,200/year per fixture but offer longer lifespans (15+ years) in corrosive environments.
Case Study:
A 2024 upgrade at a Texas ethylene plant replaced Ex d halogen lamps with IS-certified LEDs in Zone 0, achieving 50% energy savings and eliminating explosion-proof conduit costs. However, high-bay lighting in Zone 1 retained Ex d fixtures due to power demands.
4. Material Innovations Bridging the Gap
A. Hybrid Solutions
Ceramic-Coated Ex d Housings: Combine explosion containment with IS-grade thermal management, reducing surface temperatures to <135°C (T4 rating) for use in Zone 1 hydrogen sulfide zones.
IoT-Enabled IS Sensors: Monitor gas leaks while drawing <1W, complying with both ATEX and IECEx standards.
B. Emerging Technologies
Self-Healing Polymers: Automatically repair cracks in Ex d enclosures caused by thermal stress, extending maintenance intervals by 40%.
Graphene-Enhanced Barriers: Improve heat dissipation in IS systems, enabling 20% higher power thresholds without compromising safety.
5. Future Trends: Smart Integration and Sustainability
Digital Twins: Simulate IS/Ex d system performance under extreme conditions (e.g., -50°C Arctic LNG terminals), cutting physical testing costs by 35%.
Bio-Based Flame Retardants: Replace toxic additives in Ex d enclosures, aligning with EU REACH regulations.